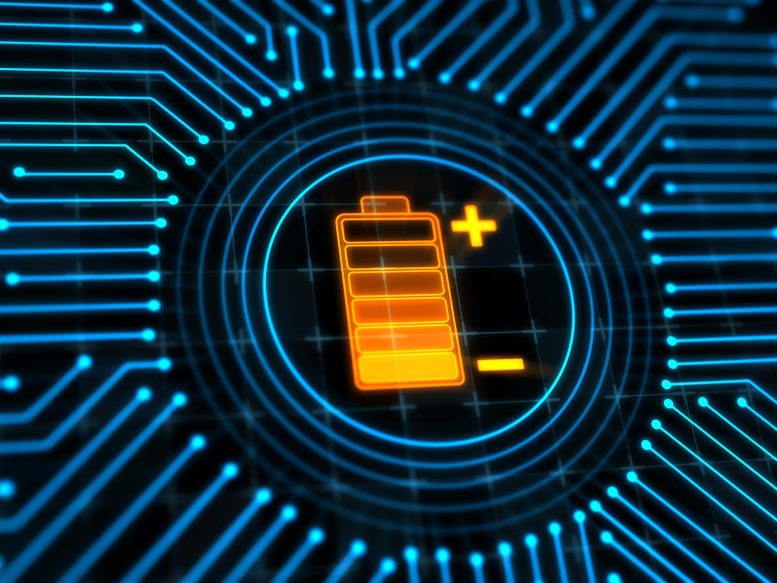
University of Missouri researchers are striving to transform solid-state battery performance by integrating advanced imaging techniques with ultra-thin coatings.
From electric vehicles to wireless earbuds, traditional lithium-ion batteries power our daily lives with their fast charging and high energy storage capabilities. However, they rely on a liquid electrolyte, which can catch fire if damaged or overheated.
Researchers at the University of Missouri may have a solution. Assistant Professor Matthias Young and his team are exploring the use of solid electrolytes instead of liquids or gels to develop solid-state batteries, which are both safer and more energy-efficient.
The Challenge of the Interphase Layer
“When the solid electrolyte touches the cathode, it reacts and forms an interphase layer that’s about 100 nanometers thick — 1,000 times smaller than the width of a single human hair,” said Young, who has joint appointments in Mizzou’s College of Engineering and College of Arts and Science. “This layer blocks the lithium ions and electrons from moving easily, increasing resistance and hurting battery performance.”
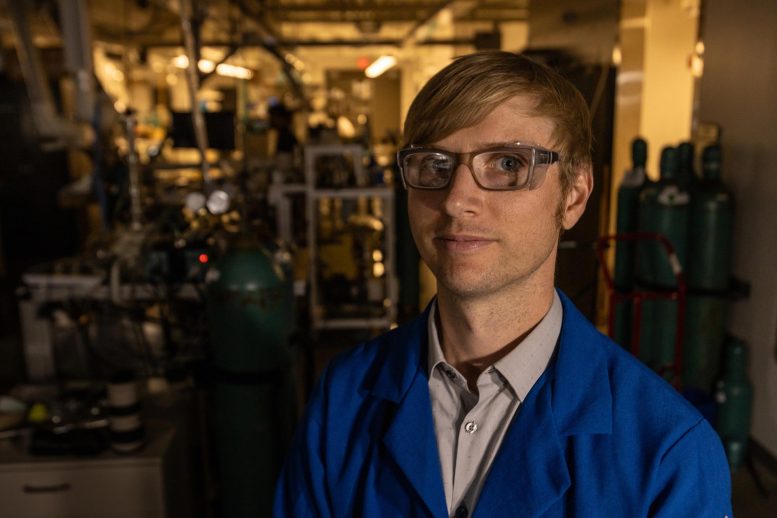
Understanding this issue with solid-state batteries — and how to overcome it — has vexed scientists for more than a decade.
Young’s team tackled the problem by better understanding the root cause.
Using four-dimensional scanning transmission electron microscopy (4D STEM), the researchers examined the atomic structure of the battery without taking it apart — a revolutionary breakthrough for the field. This novel process allowed them to gain a fundamental understanding of the chemical reactions happening inside batteries, ultimately determining that the interphase layer was the culprit.
A potential solution
Young’s lab specializes in thin-films formed by a vapor-phase deposition process known as oxidative molecular layer deposition (oMLD). Now, he plans to test whether his lab’s thin-film materials can form protective coatings to prevent the solid electrolyte and cathode materials from reacting with each other.
“The coatings need to be thin enough to prevent reactions but not so thick that they block lithium-ion flow,” he said. “We aim to maintain the high-performance characteristics of the solid electrolyte and cathode materials. Our goal is to use these materials together without sacrificing their performance for the sake of compatibility.”
This carefully engineered approach at the <span class="glossaryLink" aria-describedby="tt" data-cmtooltip="
” data-gt-translate-attributes=”[{"attribute":"data-cmtooltip", "format":"html"}]” tabindex=”0″ role=”link”>nanoscale level will help ensure these materials work together seamlessly — making solid-state batteries one step closer to reality.
Reference: “Understanding Cathode–Electrolyte Interphase Formation in Solid State Li-Ion Batteries via 4D-STEM” by Nikhila C. Paranamana, Andreas Werbrouck, Amit K. Datta, Xiaoqing He and Matthias J. Young, 23 December 2024, Advanced Energy Materials.
DOI: 10.1002/aenm.202403904